Do it same, but better!
DOTTIKON EXKLUSIVE SYNTHESIS AG setzt beim Bau zweier neuer Anlagen auf bewährte Konzepte, modernste Technik und Innovation.
Greenfield Projekte bieten eine gute Gelegenheit, bewährte Konzepte neu zu denken und die neuesten technischen Fortschritte einzubeziehen. Unser langjähriger Kunde DOTTIKON EXCLUSIVE SYNTHESIS AG setzt beim Bau zweier neuer Anlagen auf grüner Wiese auf erprobte Lösungen, strebt jedoch nach Innovation. CTE unterstützt mit Expertise und liefert das innovative Design für Automation, OT und EMSR aus einer Hand.
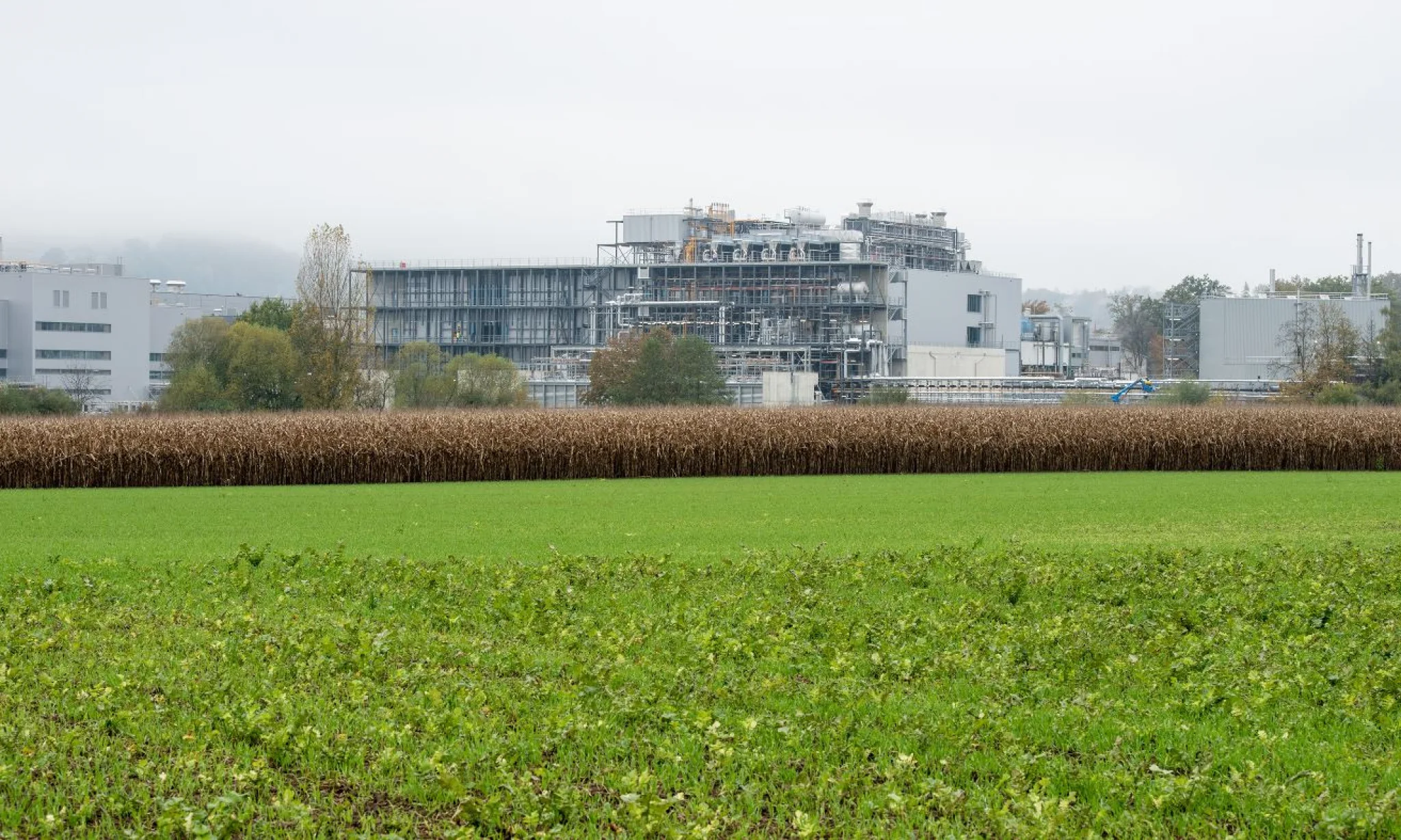
Um neue Wege zu beschreiten, bieten Greenfield Projekte eine gute Chance. So auch bei DOTTIKON EXCLUSIVE SYNTHESIS AG. Das Unternehmen trifft schon seit den 90er Jahren stets zukunftsweisende Entscheidungen. Sei es durch den Einsatz von Provox als erstes Leitsystem oder der frühen Einführung des kompakten DeltaV-Systems in der Schweiz Anfang der 2000er Jahre – DOTTIKON EXCLUSIVE SYNTHESIS AG war immer einen Schritt voraus.